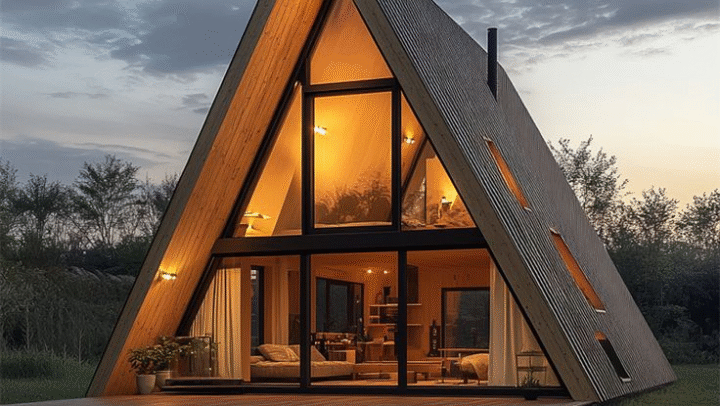
Discover Prefabricated Holiday Cottages by Thermoteq Prefab Houses Ltd
7 Good Reasons to Choose Thermoteq’s Exceptional Prefabricated Holiday Cottages in Kenya In today's fast-moving world, more people are looking for affordable...
0
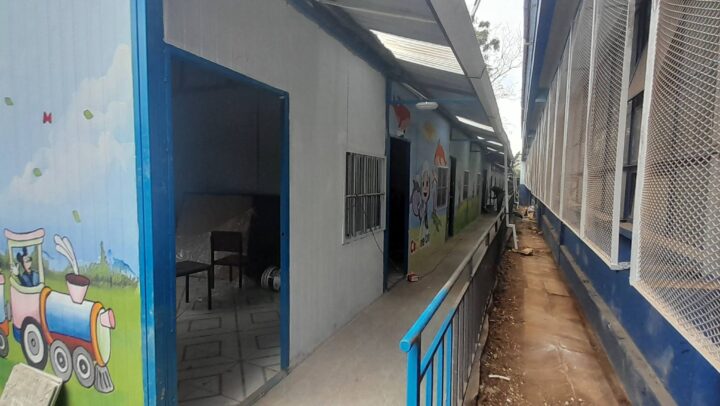
Low Cost School Building Construction in Kenya: A Modern Solution to Schools.
In Kenya, the demand for high-quality, cost-effective school facilities is growing as the education sector expands to accommodate increasing student populations...
0
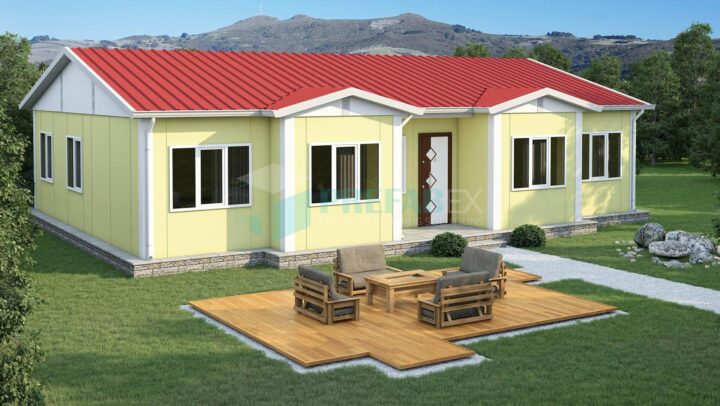
Modern Affordable 2 Bedroom House Construction in Kenya Using EPS Technology
It is a great opportunity for Kenyans who plan to invest in modern and affordable 2 bedroom house construction as well as 3 bedroom modern house construction. T...
0
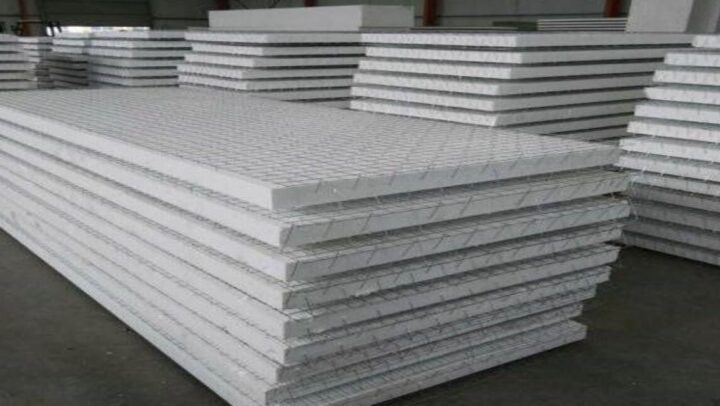
Why More Developers Use EPS Panels in Kenya?
The construction industry in Kenya is witnessing a notable shift toward sustainable, cost-effective, and efficient building solutions. One innovation leading th...
0
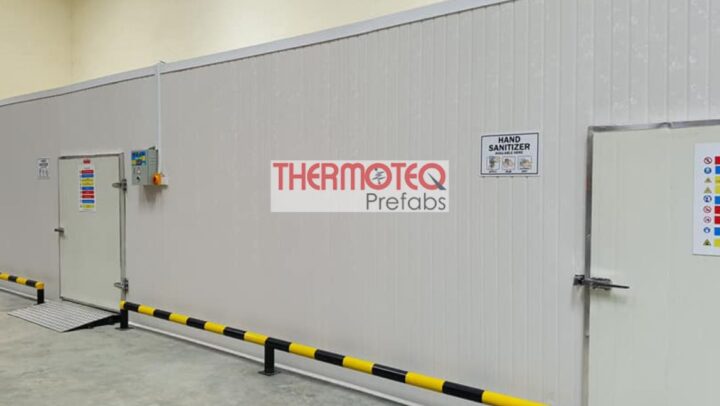
Finest Cold Room Installation in Kenya by Top Industry Experts
When it comes to high-quality cold room installation in Kenya, Thermoteq Limited stands out as a leading provider with extensive experience in designing, buildi...
0
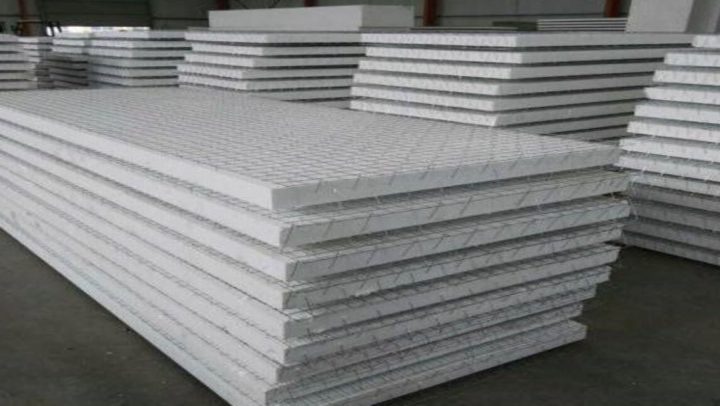
EPS Panels Manufacturers: Sandwich Panels Kenya
When choosing the right EPS panels manufacturers, there are several factors to consider to ensure you select reliable and reputable EPS panels suppliers. EPS pa...
0
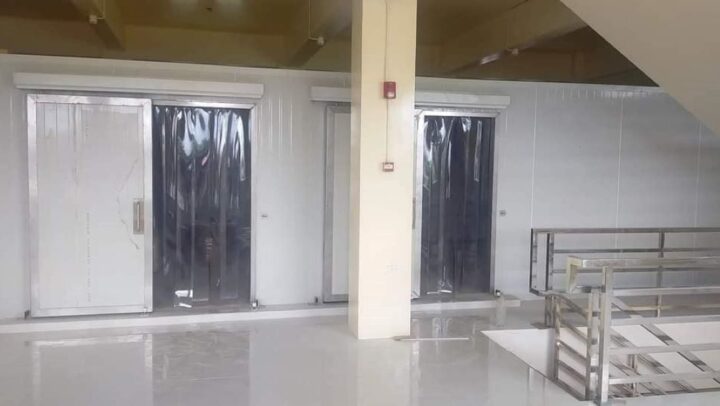
Cold Rooms Manufacturers in Kenya: Cold Rooms Prices
Cold rooms manufacturers in Kenya provide a range of services related to the design, fabrication, and installation of cold rooms or refrigerated storage systems...
0
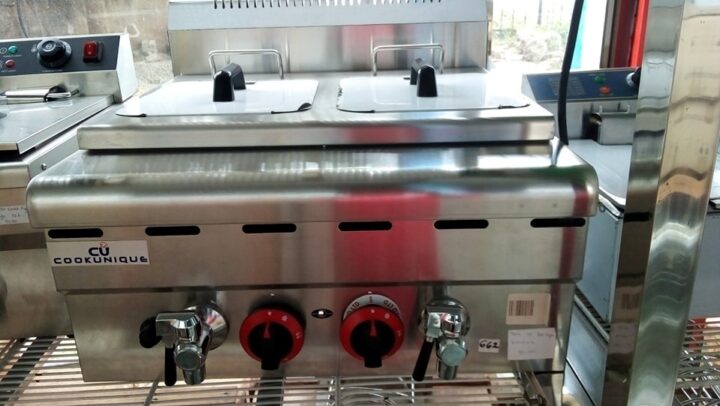
Commercial Kitchen Equipment: Modern Kitchen Kenya
Thermoteq Limited specializes in quality design, installation and supply of Commercial Kitchen Equipment in Kenya and East Africa. Commercial kitchen equipment...
0
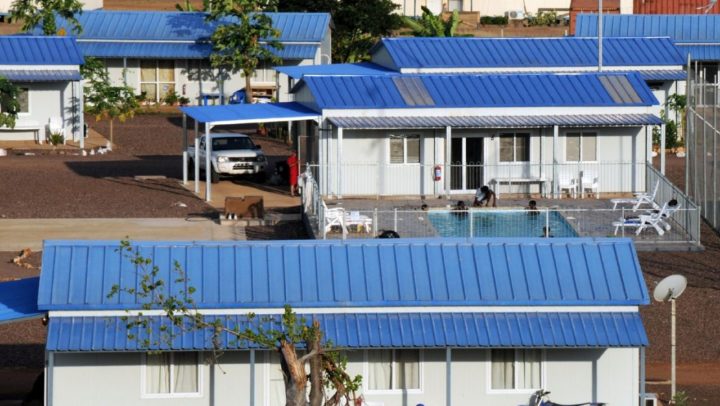
Low Cost Houses in Kenya
Low Cost Houses in Kenya Low cost houses in Kenya, also known as affordable housing or low-income housing, refer to properties that are designed to be affordab...
0